The textile world is buzzing after German researchers successfully spun fibers from lignin and cellulose, offering progress toward bio-based textiles. But here’s the twist – while the tech breakthrough is real, the supply chain story behind it reveals just how complex the journey from lab to closet really is.
The Fiber Breakthrough That Has Everyone Talking
The German Institutes for Textile and Fibre Research (DITF) successfully spun fibres from lignin, blended with cellulose during the BioFibreLoop project’s first year. This isn’t just another eco-friendly textile claim – it’s actual functional fabric that offers potential replacement of petroleum-based textiles with renewable alternatives.
The magic happens in a process called thermoplastic spinning, where lignin blended with a suitable cellulose that increases suppleness and strength, in three development stages creates fibers with a slightly brownish, fine, and smooth continuous fibres exhibit a slightly shimmering sheen. This offers a renewable alternative to petroleum-based outdoor fabrics.
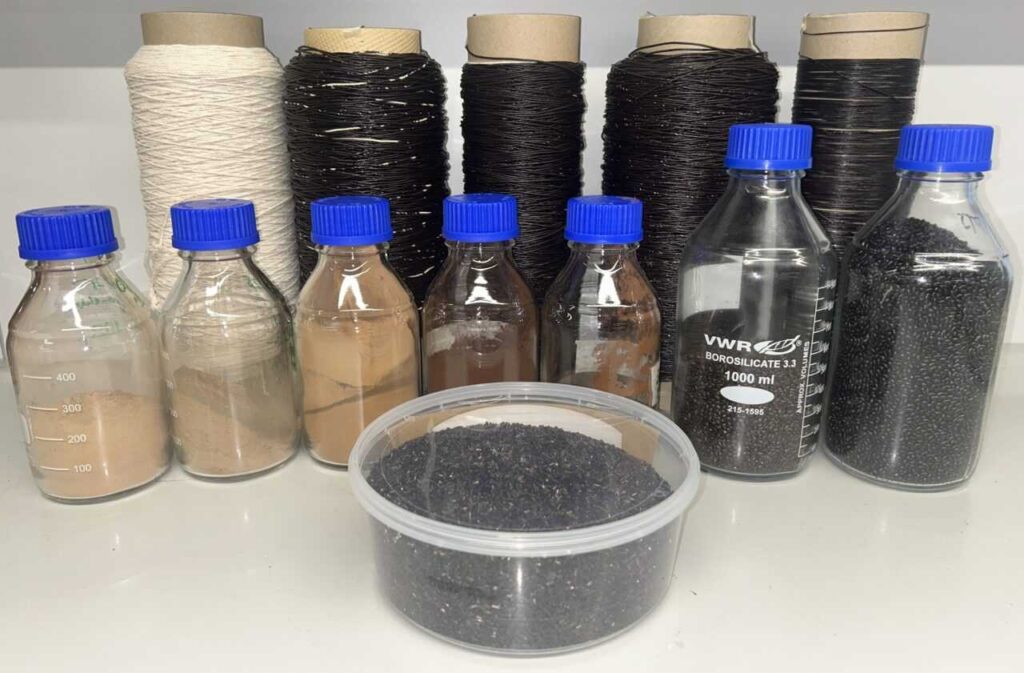
What Makes These Fibers Special
The BioFibreLoop project isn’t just creating any old bio-based fabric. These textiles pack serious functionality. A thin lignin coating is applied to the textile surface to protect against liquids, gases, UV light, and bacteria. The coating gets an extra boost through a novel, highly environmentally friendly surface treatment to give the lignin coating increased water and oil repellence beyond its natural material properties.
The project includes ongoing work on life cycle assessment (LCA) and biodegradability assessments as part of Work Package 4. EN 13432 biodegradability criteria are targeted, with testing underway.
The Supply Chain Reality Check
Here’s where the story gets interesting. While DITF nailed the technical challenge, sourcing the raw materials proved trickier than expected. Several small companies that have developed high-quality lignin variants in recent years have had to close their businesses, creating supply headaches for the project.
The problem is that ‘Basal lignin’, which refers to lignin that has been extracted but not further modified, varies widely in properties and therefore also in quality depending on the extraction process. It’s like trying to bake bread with flour that changes consistency batch to batch – possible, but requires serious skill and flexibility.
To tackle this, DITF conducted a thorough analysis of available suppliers. This included testing material suitability using rheological analyses, particularly the ability to draw fibres in thermoplastic spinning process and film forming in coating. Basically, they had to become lignin detectives, hunting down supplies that would actually work for textile production.
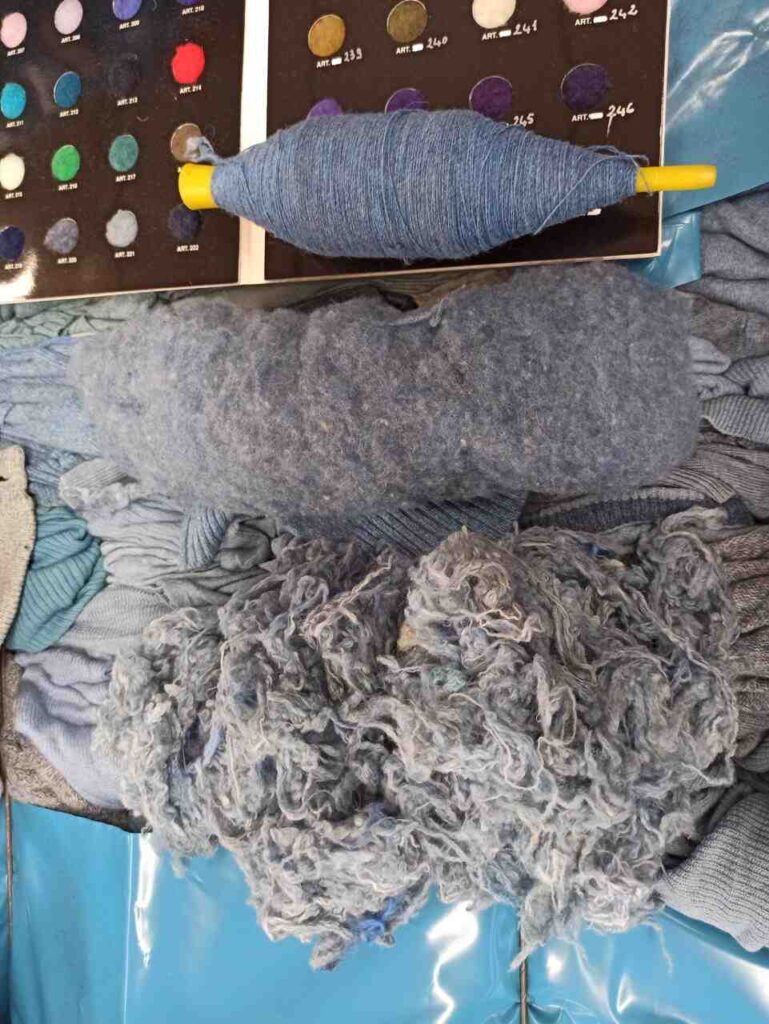
Cost Reality: The Economics of Going Green
Let’s talk money, because sustainable fashion only works if it’s commercially viable. The project aims to explore cost-competitiveness through scale and process optimization.
In the carbon fiber market, research organizations are exploring cost-effective lignin-based carbon fiber alternatives, highlighting the potential economic advantages of this approach.
The Biorefinery Solution on the Horizon
The supply shortage might be temporary. TNO’s Fabiola demonstration plant (1 M kg biomass/year) is being developed as a significant biorefinery initiative, offering potential for lignin suppliers. This next-generation biorefinery can extract high-quality lignin from biomass at significantly higher yields than previously possible.
Thomas Stegmaier, BioFibreLoop’s Technical Coordinator, is optimistic about market-driven solutions. “Our good research results on the use of lignin in textile products together with the great market potential will strongly motivate the establishment of biorefineries for suitable lignin variants in Europe,” he said.
Market Numbers That Matter
The timing couldn’t be better for lignin-based materials. The global lignin products market size was valued at USD 1.85 billion in 2024 and is projected to reach from USD 1.92 billion in 2025 to USD 2.67 billion by 2033, growing at a CAGR of 4.2% during the forecast period according to Straits Research.
Lignin is produced as a by-product in pulp and paper facilities worldwide, with a very small percentage currently used for specialty chemicals and value-added products. The potential for increased utilization in various applications shows additional growth opportunities.
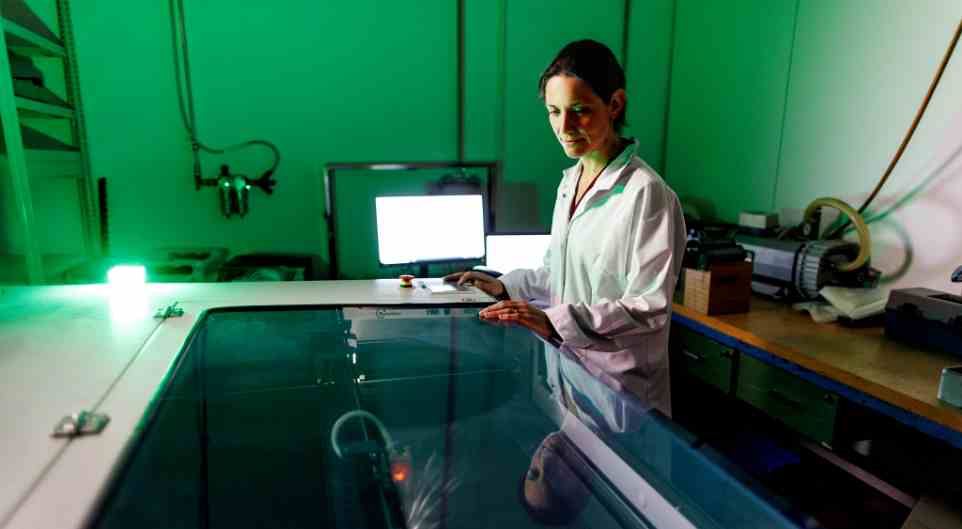
Policy Support Driving Innovation
European funding is backing this transformation in a big way. The Circular Bio-based Europe Joint Undertaking (CBE JU) has selected 31 innovative projects to receive nearly €215.5 million in funding, with €172 million will be dedicated to advancing competitive circular bio-based industries in Europe across 13 topics in 2025.
The policy framework is also pushing demand. The EU’s Circular Economy Action Plan (CEAP) promotes textile waste reduction and circular approaches through the EU Strategy for Sustainable & Circular Textiles, with specific targets for textile recycling and reuse currently under development rather than being mandated at a specific percentage.
Technical Innovation Behind the Scenes
The BioFibreLoop team isn’t just swapping materials – they’re reimagining how textiles get their functional properties. The project uses a novel, laser-based embossing process to create water and oil-repellent surfaces by mimicking natural structures found on plants and fish.
The major challenge now lies in transferring these structures to the surfaces of the lignin coating using a novel, laser-based embossing process. The laboratories of ALPHANOV in France and the DITF are already conducting intensive research into metallic surfaces for transfer, special laser technologies, and the many variations of embossing techniques.
The result? Functional outdoor clothing that repels water and oil without relying on harmful per- and polyfluoroalkyl substances (PFAS) that are increasingly banned across Europe.
What This Means for Your Closet
BioFibreLoop has ambitious goals – they want to see its bio-based textiles adopted by 20% of the textile industry. If successful, this would reshape the outdoor and workwear markets significantly. The project spans 42 months (start: 01 June 2024), a participation of 13 partners and a total budget of 7 million euros (funded by the EU with 6.5 million euros).
Similar Posts
The project targets specific markets: garments for workwear, activewear, and outdoor products. These aren’t niche applications – workwear represents an important European market that values durability and performance over fashion trends.
Competition and Context
The competitive landscape includes both technical innovation and supply chain development. Various European research institutions are working on bio-based alternatives to conventional textiles and materials, with different approaches to sustainability challenges.
Environmental Impact Beyond Carbon
The environmental benefits extend beyond just carbon footprint reduction. Traditional textile production relies heavily on petrochemicals and generates significant waste.
Lignin-based textiles offer a different path, similar to how sustainable fashion is exploring alternatives like mushroom-based materials. Since lignin is generated as a waste product from the paper and ethanol production, using it for textiles creates value from what would otherwise be burned for low-grade energy – a concept that’s also being explored in renewable energy storage.
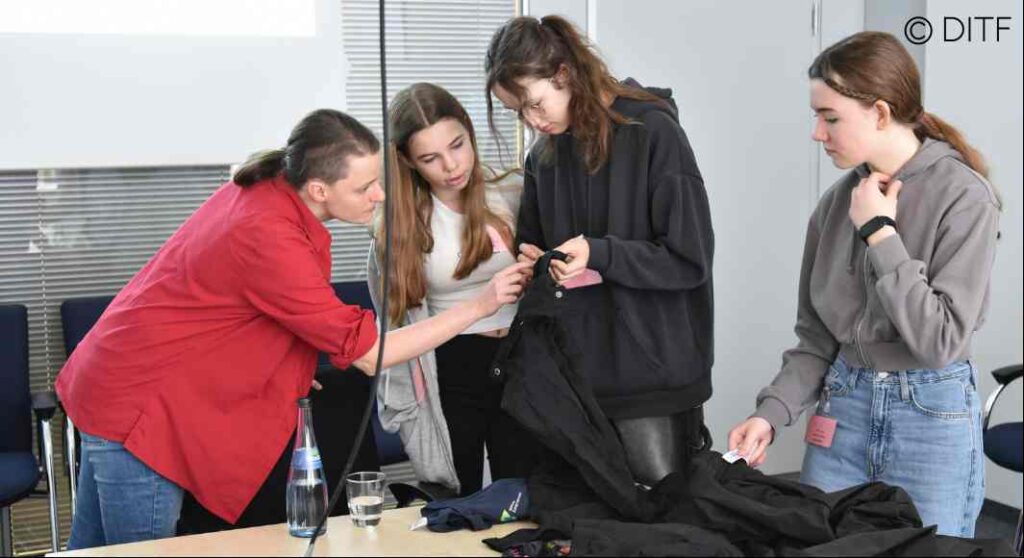
Scaling Challenges and Opportunities
The path from laboratory success to mainstream adoption involves scaling both production and supply chains. To meet future demand, expanding biorefinery capacity would be needed beyond the current demonstration facilities.
The economic incentives are aligning. As more lignin-based products might enter the market, also supported by European legislation favouring bio-based products, there is a high potential to build resilient, circular supply networks.
For brands and manufacturers, this represents both opportunity and risk, particularly as consumers increasingly seek sustainable alternatives to traditional materials. Early movers could capture market share in the growing sustainable textiles segment, while late adopters might find themselves scrambling to meet increasingly strict environmental regulations.
What Comes Next
The BioFibreLoop project continues through 2027, with three industrial demonstration projects in Austria, the Czech Republic and Germany planned to prove commercial viability. Success would establish a process under development for the production of recyclable functional textiles.
The demonstration phase will evaluate performance in work and outdoor environments. These aren’t laboratory conditions – they’re the real-world settings of construction sites, hiking trails, and industrial facilities where functional clothing must perform reliably.
Meanwhile, supply chain development continues. The combination of new biorefineries, improved extraction processes, and growing market demand could solve the current sourcing challenges that have slowed initial commercialization.
The BioFibreLoop story illustrates both the promise and complexity of sustainable textile innovation. Technical breakthroughs are just the beginning – real change requires aligned supply chains, supportive policy, and market acceptance. But with European funding, regulatory pressure, and growing consumer demand for sustainable alternatives, lignin-based textiles might just become the foundation for a more circular fashion industry.
The project covered BioFibreLoop’s technical achievements, supply chain challenges, cost considerations, policy support, and market potential. Current developments include successful fiber spinning at DITF, upcoming biorefinery commissioning, and substantial European funding allocation for bio-based industries. The analysis encompassed regulatory frameworks, environmental benefits, competitive landscape, and scaling requirements for commercial deployment.