Researchers from RMIT University have developed a new type of “green concrete” that contains twice the amount of recycled coal ash compared to existing low-carbon concrete and requires half the amount of cement, potentially extending its lifespan beyond that of ordinary Portland cement concrete.
While it is true that there are already companies that manufacture eco-friendly concrete, they only eliminate 40% of the cement, a considerable amount, but apparently not enough to eliminate the negative impact that this material still has on the environment.
A team from RMIT has been collaborating with the Australian Coal Ash Association and AGL Loy Yang Power Station to better utilize this questionable asset and to attempt to increase the coal ash content to replace over 80% of the cement.
This is good news considering that cement production alone accounts for 8% of global carbon emissions, and concrete, which typically uses a large amount of material, is increasingly in demand.
Dr. Chamila Gunasekara, project leader at RMIT University, remarked, “Our addition of nano additives to modify the concrete’s chemistry allows more fly ash to be added without compromising engineering performance.”
Coal ash is abundantly present around coal-fired power plants. In fact, to say so might be an understatement—globally, power plants generate about 1.2 billion tons of coal ash annually, with coal ash constituting nearly 20% of all waste in Australia alone. This is a staggering figure, and it’s certain that coal ash will continue to be plentiful for a considerable time during the transition to renewable energy.
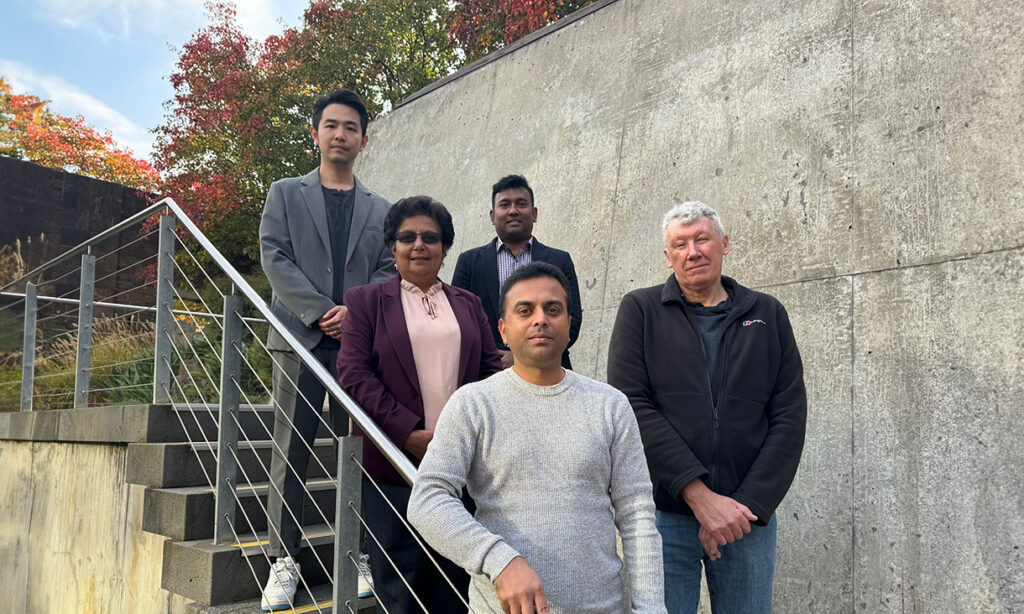
After months of work, the engineers at RMIT University have managed to replace 80% of the cement in the concrete with coal fly ash. The eco-friendly and resistant concrete developed by RMIT University, along with the Loy Yang power station of AGL and the Australian Ash Development Association, is composed of a mixture of low-calcium fly ash, with 18% hydrated lime, and 3% nano silica acting as strengthening agents. After various research efforts, they realized that the combination of these materials makes eco-friendly concrete much stronger than any other type.
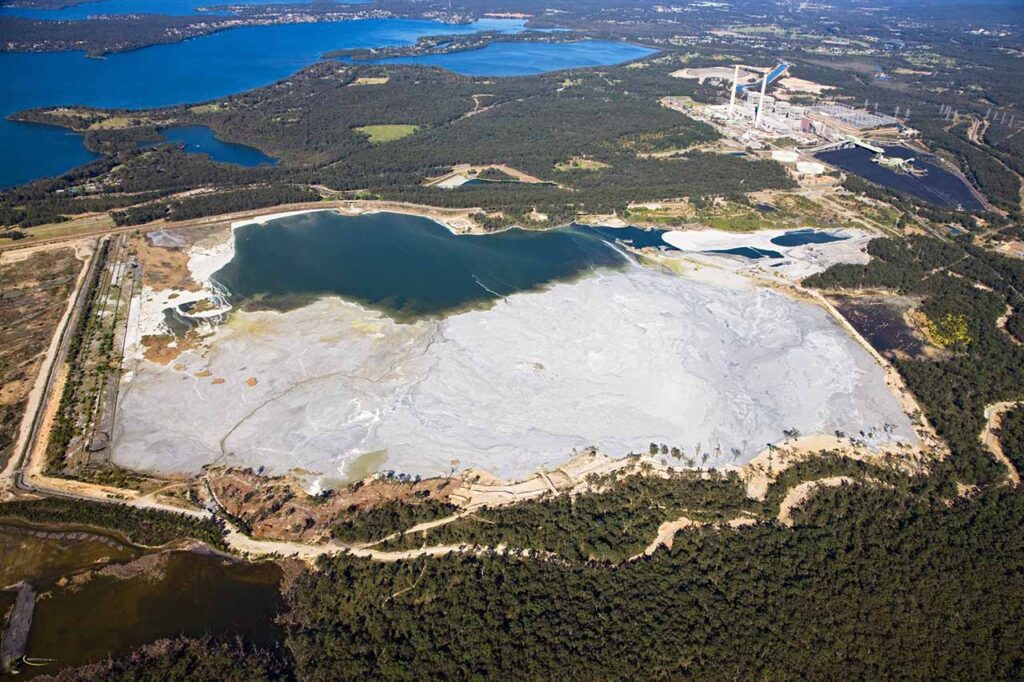
According to a 2022 UN report, around 50 billion metric tons of sand are extracted each year, mostly for concrete production. Its extraction is often environmentally destructive and is becoming increasingly scarce. Cement production, which involves heating a mixture of limestone and clay to about 1,500 degrees Celsius, is responsible for the majority of concrete emissions.
Similar Posts
Dr Yuguo Yu, an expert in virtual computational mechanics at RMIT, explained, “We’ve now created a physics-based model to predict how the low-carbon concrete will perform over time, which offers us opportunities to reverse engineer and optimise mixes from numerical insights.”
This promising development was recently presented through the prestigious journal Cement and Concrete Research, describing how various ingredients in the new low-carbon concrete interact over time.
Additionally, the use of low-calcium fly ash in concrete also helps combat climate change. Lead researcher, Dr. Chamila Gunasekara, explained, “The inclusion of ultra-fine nano additives significantly enhances the material by increasing density and compactness.” He adds, ” how the quick-setting nano additives in the mix act as a performance booster during the early stages of setting, compensating for the large amounts of slower-setting fly ash and pond ash in our mixes.”
What’s more, the team noted that this technology doesn’t require fine “fly ash” specifically and seems to be equally effective with lower grade “pond ash.” They have already made and tested structural concrete beams using the latter and have been certified to Australian engineering performance standards.
“It’s exciting that preliminary results show similar performance with lower-grade pond ash, potentially opening a whole new hugely underutilised resource for cement replacement,” Gunasekara stated.” These ash ponds risk becoming an environmental hazard, and the ability to repurpose this ash in construction materials at scale would be a massive win,” he added.
The project for the use of this eco-friendly concrete is still ongoing, and RMIT researchers are now working with Hokkaido University on a system (specifically, software) that allows them to check and forecast the performance of this type of material over time. They hope that this software will also be useful for testing other materials.