In German laboratories, plastic bottle caps that once held your morning milk are being reborn as precision-engineered components through an innovative recycling process that converts post-consumer packaging waste into high-purity 3D printing filaments.
Every year, some 5.6 million metric tons of plastic packaging winds up in household waste in Germany after being used just once. While Germany achieved a plastic packaging recycling rate of 68.9% in 2023, significant volumes of plastic waste continue rising, having approximately tripled across Germany over the past 30 years. Where German households produced 2.1 million metric tons of plastic waste in 1994, the figure had risen to 5.6 million by 2023.
The Fraunhofer Institute for Manufacturing Technology and Advanced Materials (IFAM) and Hochschule Bremen have developed a method to transform this mounting waste challenge into a valuable resource for additive manufacturing. Their process achieves something industry experts considered extremely difficult: converting dirty, mixed post-consumer plastic waste into filaments pure enough for commercial 3D printing, advancing beyond traditional mechanical recycling approaches.
The Complexity of Post-Consumer Plastic Recycling
“But it is much harder to recycle post-consumer waste than plastic residue left over from industrial production,” said Dr. Silke Eckardt, a professor focusing on sustainable energy systems and resource efficiency at Hochschule Bremen – City University of Applied Sciences (HSB). “After all, these materials are not only highly heterogeneous but generally also dirty.”
Industrial plastic waste arrives at recycling facilities already sorted and relatively clean. Post-consumer packaging waste presents a different challenge entirely. Food residues, labels, adhesives, and multiple plastic types get mixed together in household recycling bins. While Germany has achieved high recycling rates for plastic packaging at 68.9%, traditional recycling methods struggle to achieve the ultra-high purity levels required for advanced applications like 3D printing filaments.
“Since the waste is supposed to be recycled for use in 3D printing, it has to meet very stringent requirements for aspects such as purity, shape, and size,” said Dr. Dirk Godlinski, a project manager in the Composite Technology working group at Fraunhofer IFAM.
Advanced Sorting Achieves 99.8% Purity
The research team sourced polypropylene waste from a commercial sorting plant that processes packaging waste. At HSB’s Laboratories for Circular Economy, they implemented a multi-stage purification process that combines mechanical and optical sorting technologies.
The material was ground, washed, and purified using float-sink separation and near-infrared technology, achieving a purity level of over 99.8 per cent. Float-sink separation exploits density differences to remove heavier contaminants, while near-infrared (NIR) spectroscopy identifies and rejects foreign polymers like PET and PVC that would compromise filament quality.
This 99.8% purity level matches that of virgin polypropylene, creating recycled material suitable for demanding applications. The cleaned polypropylene flakes then moved to Fraunhofer IFAM for the next phase of processing.
Precision Compounding Creates Printable Filaments
The research scientist and his team produced a solid plastic strand. First, they processed the flakes of recycled polypropylene in an industrial extruder at Fraunhofer IFAM. The material was combined there, mixed using different extruder screw geometries, then melted at temperatures greater than 200 degrees Celsius and extruded.
“The expertise consists in precisely adjusting the various mechanical screws, temperatures, pressures and speeds along the production process so the final product is homogeneous polypropylene,” Godlinski explains.
The extrusion process requires precise control of multiple variables. Screw geometries determine mixing efficiency, while temperature profiles ensure complete melting without thermal degradation. For further processing in 3D printing, for example, the strand must be round and consistent in diameter over its entire length, with a smooth surface.
The researchers succeeded in this: The gray plastic strand, about two millimeters thick, was able to be used directly as a filament in a commercial 3D printer. By now, Godlinski and his team have successfully printed their first components, including caps.
Similar Posts
Meeting European Recycling Mandates
This breakthrough arrives as European regulations create new demands for recycled content in packaging. The EU Packaging and Packaging Waste Regulation (PPWR), which entered into force on February 11, 2025 but applies from August 2026, establishes mandatory recycled content targets that will reshape plastic manufacturing across Europe.
By 2030 the minimum levels of recycled material in plastic packaging will increase to 30% for contact-sensitive PET packaging, 10% for contact-sensitive packaging other than PET, 30% for single-use beverage bottles and 35% for all other packaging. The requirement for 2035 is 25 to 65 percent recycled materials.
The PPWR entered into force on 11 February 2025 and its general date of application is 18 months after that. This regulatory timeline, with implementation beginning in August 2026, creates urgent demand for reliable sources of high-quality recycled plastic materials.
Market Potential and Future Applications
The 3D printing filament market presents substantial opportunities for recycled materials. The global 3D printing filament market size was valued at USD 1,605.75 million in 2024. It is projected to reach from USD 1,984.07 million to USD 13,782.06 million by 2033, growing at a CAGR of 27.41% during the forecast period (2025-2033).
The market is witnessing a strong shift toward sustainable and eco-friendly materials. As industries move toward more responsible manufacturing, bioplastics and recycled materials are becoming increasingly popular in 3D printing applications.
Godlinski notes that plastics can be further refined, for example, by introducing additives such as glass fibers during compounding. This makes it possible to produce even very high-quality components for use in fields such as aviation and the automotive industry.
Glass fiber reinforcement could enable recycled polypropylene filaments to compete with virgin materials in structural applications. Automotive manufacturers increasingly use 3D printing for both prototyping and low-volume production parts, creating demand for materials that combine sustainability with performance.
Energy and Resource Conservation
“The more waste we reuse and recycle, the more energy and resources we can conserve,” Godlinski agreed. While specific life cycle assessment data for this process remains unpublished, comparative studies suggest recycled polypropylene typically reduces carbon footprint by approximately 25% compared to virgin material production.
The energy savings come from avoiding the petroleum extraction, refining, and polymerization processes required for virgin plastic production. Instead, the recycling process requires only collection, sorting, cleaning, and reprocessing – operations with significantly lower energy requirements.
Technical Challenges and Solutions
The transition from waste to high-quality filament requires overcoming several technical hurdles. Moisture control proves critical, as polypropylene must be dried below 0.1% moisture content before extrusion to prevent hydrolytic degradation during melting.
Temperature control throughout the process prevents molecular weight reduction that would compromise mechanical properties. The research team optimized processing parameters to maintain the polymer structure while achieving the flow characteristics needed for consistent filament production.
Surface quality emerges as another crucial factor. 3D printers require filaments with smooth surfaces and consistent diameter to prevent nozzle blockages and ensure reliable feeding. The Fraunhofer process achieves these requirements through precise die design and controlled cooling rates.
Scaling Production
This marks the conclusion of the feasibility study by HSB and Fraunhofer IFAM. The researchers are now optimizing the production process. Moving from laboratory-scale processing to industrial production will require scaling up sorting and extrusion equipment while maintaining quality standards.
Fraunhofer IVV operates pilot-scale plastic recycling equipment with batch operations of 100-250 liters producing up to 20 kg of recyclates, providing a pathway for process scale-up. The economics of industrial-scale production will depend on establishing reliable feedstock supplies and achieving processing costs competitive with virgin materials.
Global Context and Future Outlook
Germany’s experience with rising packaging waste reflects global trends. The development of effective post-consumer plastic recycling technologies becomes increasingly urgent as waste volumes continue growing worldwide, despite improved recycling rates in advanced economies.
Each European generated 188.7 kg of packaging waste in 2021, a figure that is expected to increase to 209 kg in 2030 without additional measures. Effective recycling technologies like the Fraunhofer process offer pathways to manage this growing waste stream while creating value-added products.
The success of this German project could influence recycling practices globally. Countries implementing extended producer responsibility systems and recycled content mandates will need proven technologies for converting post-consumer waste into high-value applications.
Ideas for follow-up projects have already been floated. The research team plans to explore additional polymer types and develop composite formulations that could expand applications into aerospace and automotive sectors where performance requirements are particularly demanding.
Implementation Roadmap
The feasibility study validated the technical approach, but commercial implementation requires additional development. Scaling the sorting process to handle larger volumes while maintaining 99.8% purity levels presents engineering challenges that will need systematic solutions.
Integration with existing waste management systems offers another pathway for implementation. Municipal recycling programs could potentially incorporate this advanced sorting technology to upgrade the quality of recovered plastics, creating higher-value end markets.
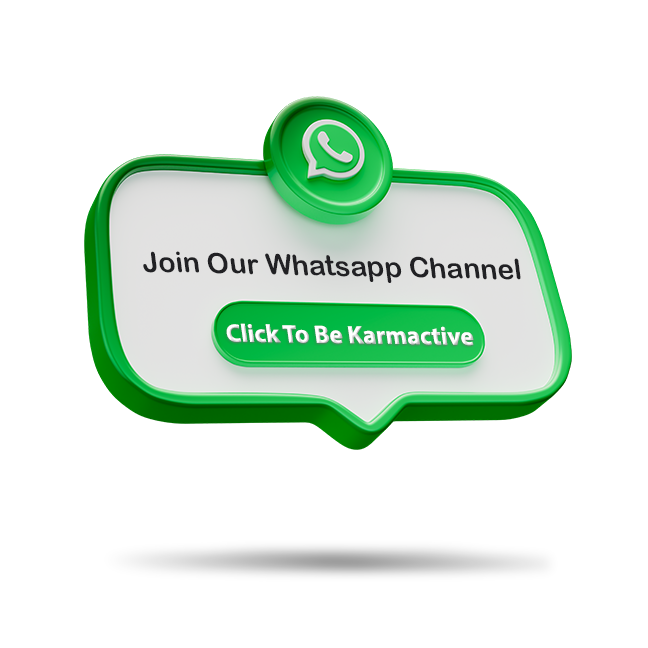
Quality assurance systems become essential for commercial production. Consistent filament properties require continuous monitoring of purity levels, diameter tolerance, and mechanical characteristics throughout production runs.
The project completed its feasibility phase in early 2025, with optimization work continuing. The research demonstrates that post-consumer plastic packaging waste can be converted into 3D printing filaments meeting commercial quality standards. The combination of advanced sorting technologies, precision compounding, and growing regulatory demand for recycled content creates favorable conditions for scaling this approach to industrial levels.