Bangladesh’s garment makers are fighting to keep production lines running as gas shortages throttle operations. In key industrial hubs, many factories now operate at just 30-40% capacity, threatening the sector that accounts for more than 80% of the country’s export earnings.
“We’re in survival mode,” explains Mohammad Hatem, president of the Bangladesh Knitwear Manufacturers and Exporters Association (BKMEA). “When your machines need 10 PSI of gas pressure but you’re getting only 1-2 PSI, you simply can’t deliver orders on time.”
The numbers tell a stark story. Bangladesh faces a daily gas deficit of nearly 1,000 million cubic feet per day (mmcfd). With national demand hovering around 3,800 mmcfd against a domestic production of 2,500-2,800 mmcfd, the gap has widened as aging gas fields deplete and imports lag.
System losses compound the problem. At 13%, these inefficiencies cost the economy dearly, with each percentage point reduction potentially saving Taka 1,000 crore annually.
Financial Solutions Taking Shape
To bridge the supply gap, Bangladesh is working on multiple fronts. The World Bank has proposed a $350 million revolving letter of credit facility through its Multilateral Investment Guarantee Agency (MIGA), providing 100% guarantees for LCs issued to Petrobangla for LNG imports.
This financial mechanism comes as Bangladesh’s Advisory Council Committee on Government Purchase (ACCGP) continues approving spot-market LNG cargoes priced between $14-15 per MMBtu, translating to roughly Taka 675-690 crore per shipment.
Industry leaders have suggested a prepayment mechanism that would allow manufacturers to directly fund LNG imports in exchange for dedicated gas supply. While this model requires significant upfront capital, many factory owners see it as preferable to the production losses they’re currently absorbing.
Similar Posts:
Diversifying Supply Sources
Bangladesh has been expanding its LNG supplier base, moving beyond long-term contracts with Qatar and Oman. The government has approved procurement from additional suppliers through the spot market to increase competition and potentially lower costs.
Infrastructure improvements are also underway. Plans for both floating storage regasification units (FSRUs) and onshore LNG terminals aim to increase import capacity, though these projects require time to implement.
Trade Pressures Add Urgency
The energy crisis coincides with trade challenges. In April 2025, the US implemented a 37% tariff on Bangladeshi garment exports, though this was followed by a 90-day pause after diplomatic outreach.
“This breathing space gives us time to address our energy crisis,” notes Hatem. “But we need sustainable solutions before the 90 days expire.”
Industry analysts point out that even with the tariff challenges, Bangladesh stands to potentially gain market share from China, which faces a 125% US tariff on similar products. However, this opportunity can only be seized if the gas supply improves.
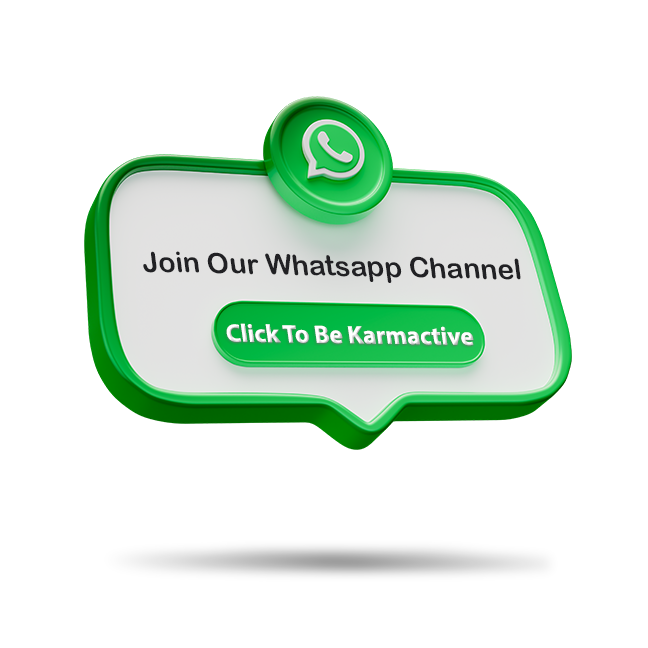
Practical Steps Forward
For factory owners grappling with the immediate crisis, several approaches offer potential relief:
- Energy efficiency upgrades can help maximize production even at lower gas pressures
- Coordinated industry consortia could pool resources for prepayment mechanisms
- Diversification of energy sources, including solar installations for non-production facilities
- Strategic production scheduling to maximize output during periods of better gas supply
The longer-term outlook depends on creating a balanced energy portfolio combining spot LNG, domestic gas expansion, and renewable solutions. Bangladesh’s plans to invite bids for 24 Bay of Bengal exploration blocks and drill 100 new wells by 2028 could extend self-reliance if successful.For Bangladesh’s garment sector, the path forward requires coordinated action across policy, infrastructure, and financing. With the right mix of immediate pragmatism and long-term vision, the industry that clothes millions worldwide can weather this energy storm and emerge more resilient on the other side.